On Tuesday November 19th, SolarSPELL completed their Fall 2019 Build Day at the ASU Polytechnic campus in Mesa. 30+ students along with faculty, staff, and student volunteers came together to create this year’s crop of 66 new units.My name is Tyler Eglen and I’m new to the team this year but was given the opportunity to reflect on this year’s build day. If you’re reading this post, maybe you’ve heard of or even participated in a build day before, so I thought we might get a new perspective on this year’s build day by following the build process of one unit from start to finish. Check out this video to go on the journey yourself.
As you can see, each SolarSPELL is the product of many hands, and even more minds and hearts! The process you see here is only a small portion of the great work that goes into producing not just a mechanical SolarSPELL, but the whole SolarSPELL program. But we’re here to talk build day, so let’s look at some of the changes this year!
- Martin Perez Comisso explains a part of the build at SolarSPELL build day, November 19, 2019. Photos taken by Jenny Dupuis.
- Whitney Geren at SolarSPELL build day, November 19, 2019. Photos taken by Jenny Dupuis.
After an early arrival and setup of tables into a classic horseshoe for factory-line style production, the team was ready for students to arrive and get to training and production. This process gets tweaked a bit each year, but we’ve also learned what works well so we can maximize efficiencies.
- Julianna Acero attaches a solar panel to the SolarSPELL model during SolarSPELL build day, November 19, 2019. Photos taken by Jenny Dupuis.
- Laura Hosman at SolarSPELL build day, November 19, 2019. Photos taken by Jenny Dupuis.
Changes: First off, a newer version of the plastic case with a more robust hinge was chosen this year. In the past, the plastic two-part hinge mechanism that keeps the internal components safe and dry could sometimes get out of place – but with the newer version, the hinge has been switched to a slightly thicker and more resilient part (it’s also very blue).
- SolarSPELL build day, November 19, 2019. Photos taken by Jenny Dupuis.
- SolarSPELL build day, November 19, 2019. Photos taken by Jenny Dupuis.
The biggest change this year was switching to a new method of combining and connecting the electronic wires from the solar panel to the voltage regulator.
- (From left) Camryn Lizik and Sairo Ramirez at SolarSPELL build day, November 19, 2019. Photos taken by Jenny Dupuis.
- Emily Sherman listens to Martin Perez Comisso’s build demonstration during the SolarSPELL build day, November 19, 2019. Photos taken by Jenny Dupuis.
The classic method for combining wires together is with a soldering iron and a metal alloy with a relatively low melting point known as solder. This is a somewhat delicate and skillful job that could bottleneck our production flow.
- Courtney Bayer at SolarSPELL build day, November 19, 2019. Photos taken by Jenny Dupuis.
- Danielle Rivera combines wires during SolarSPELL build day, November 19, 2019. Photos taken by Jenny Dupuis.
So, this year we turned to solder sleeves. This handy little product is the combination of two products, solder and heat shrink tubing. So instead of requiring a soldering iron and loose solder, this product only requires a hot air gun to perform both jobs.
- SolarSPELL build day, November 19, 2019. Photos taken by Jenny Dupuis.
- Sarah Clifford attaches solar panels to the SolarSPELL devices during the SolarSPELL build day, November 19, 2019. Photos taken by Jenny Dupuis.
Here’s the basic rundown: Two wire ends meet in the center of the tube, directly below the pre-loaded solder ring. Heat is applied and the tubing shrinks down, hugging the wire in place. After enough heat is applied the solder ring liquifies and spreads into the loose wire ends, creating a physical and electrical bond. In a few seconds it cools, re-solidifies and voila! You have a watertight, electrical and physical bond.
Once this is installed, the rest of the work is really all about locking things in place. The battery (also a newer model) and Raspberry Pi (the brains of the operation) are installed with velcro, while the solar panel is glued on with industrial strength glue that’s meant to endure no matter where it gets sent in the world. Speaking of globetrotting, this year’s batch will find themselves in South Sudan, Comoros, and East African refugee camps.
- Sara Jordan at SolarSPELL build day, November 19, 2019. Photos taken by Jenny Dupuis.
- Emily Sherman at SolarSPELL build day, November 19, 2019. Photos taken by Jenny Dupuis.
- Camryn Lizik at SolarSPELL build day, November 19, 2019. Photos taken by Jenny Dupuis.
- Yaritza Hernandez at SolarSPELL build day, November 19, 2019. Photos taken by Jenny Dupuis.
At the end of our work session, 66 new SolarSPELLS were finished!
In my eyes, SolarSPELL continues to be a project that exemplifies what global development work is about. It’s a practical and effective program that serves a global need. Yes, it faces challenges like all projects, but its effect is tangible. People are benefiting from the work of the SolarSPELL team right now. Students at ASU are getting real world experiences that regular class can’t offer them, and eager learners worldwide are getting exposed to new ideas that will empower them to make the most of their lives. It’s a win/win.
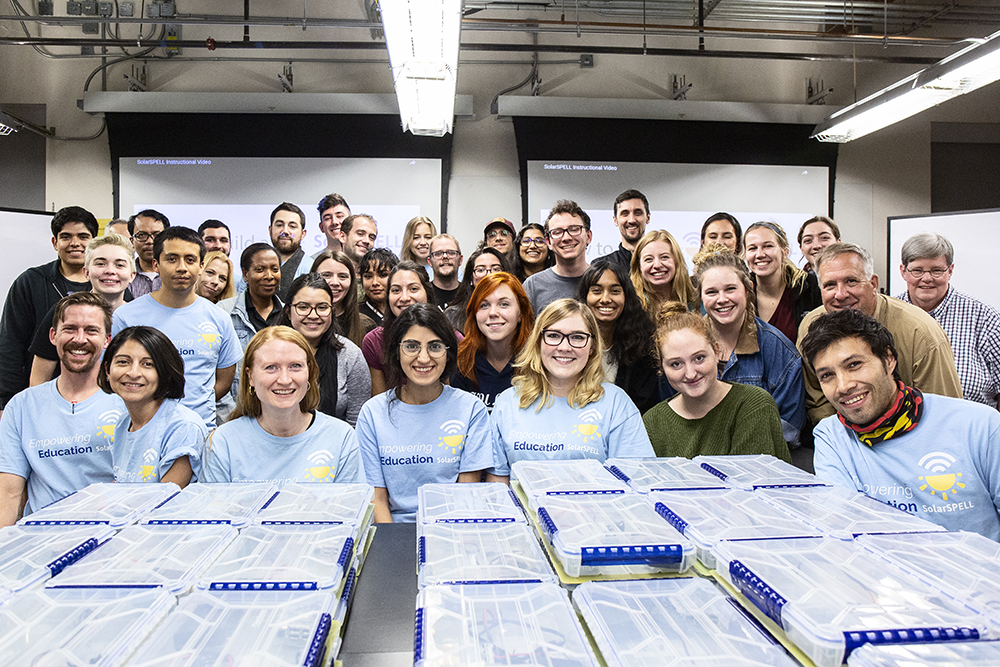
SolarSPELL build day group, November 19, 2019. Photos taken by Jenny Dupuis.
Thank you so much to Jenny Dupuis for attending our Build Day and taking the beautiful photos included in this post!